Brazed Plate Heat Exchanger
How BPHEs Work
內容文字
How BPHEs Work
Kaori's Brazed Plate Heat Exchangers (BPHE) are made by pressing a series of thin corrugated stainless steel together and brazed with copper or nickel. The soldering material is then melted in a vacuum furnace to form a seal between each of the plates. This brazing process seals the plates together making extremely durable and allows for Kaori BPHEs to perform under high working pressure and temperatures.The spaces in between the plates become flow channels with one fluid flowing in odd number channels and the other in the even number channels. Heat exchange occurs through the designed plates over a large surface area making Kaori BPHEs very efficient. Nearly all of the material is used for heat transfer making it also very compact and cost-effective.
Plate patterns are designed for performance with respect to your application. Special consideration is given when designing the width of chevron angles and height of curvature of the individual plates. Plate patterns cause high turbulence flow which significantly reduces fouling and increases heat transfer performance. After decades of research and development, Kaori has optimized plate patterns for specific applications and continues to find innovative ways to increase performance while minimizing pressure drop.
Standard BPHE flow pattern is a single pass arrangement; meaning working fluid flows in a single direction through the unit. A multi-pass arrangement is where working fluid can change its flow path and is sometimes used for low flow rates or extremely close temperature approaches. Other times, multi-pass arrangements are used to provide flexible design configurations in certain applications.
While there are many things to consider when purchasing a new BPHE with regard to optimizing design and application, a Kaori representative can help you with selecting the most suitable heat transfer solution.
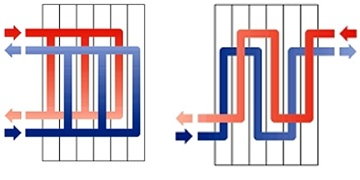